Published May 5th, 2021
In construction, soil testing refers to the process of evaluating the suitability of the soil for your building project. As we all know, soil type and quality vary greatly around the world. They can be sandy and porous, rocky, waterlogged, etcetera. Obviously, some soil types are not suitable or maybe even dangerous for construction.
This is why soil testing is almost always the first step in planning a construction project. In most places, you can’t get a building permit until the soil has been tested. And rightly so. If the soil isn’t fit to hold the type of structure you’re planning to build, it won’t only affect its stability. It can also lead to costly repairs, or worse, fatal accidents.
If you’re planning to commission soil testing for construction, here’s what you need to know:
Why is Soil Testing Important Before Construction?
It’s a well-known fact that for a structure to last, it must have a strong foundation. Aside from supporting the load of the entire building, it also helps keep it upright despite harsh weather conditions.
For a foundation to be strong, it must have depth, consistency, permanence, and stability. The last two requirements are why soil testing is important before construction work commences.
You see, the soil beneath your structure forms part of your foundation. It holds the entire load of the structure and keeps it stable and permanently anchored to the ground.
If the soil is too soft, it won’t be able to resist the force coming from the structural load. Your structure will end up sinking or breaking apart. Natural calamities like earthquakes and floods can also easily cause cracks in the soil or wash it away. This leaves the structures above it more prone to collapse and damage.
Testing the soil will help you determine the type of foundation you’ll need as well as any adjustments to the soil. It will also help you plan your structural design more accurately so as to avoid structural failures.
Who Does Soil Testing?
Soil testing is performed by soil engineers or geotechnical engineers. These professionals are licensed by the state and must have passed the NCEES exam. Most of them have also worked for or have interned for a licensed soil engineer before they can practice their profession.
You can hire them privately or ask for recommendations from your architect. There are also construction companies that offer soil testing as a separate service.
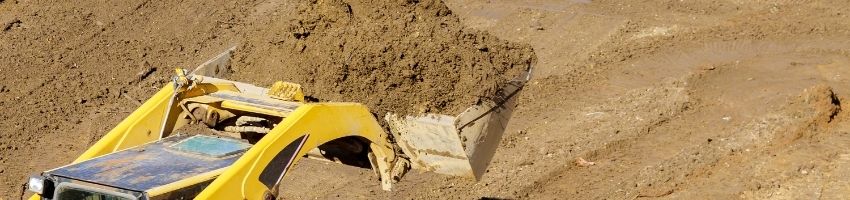
Types of Soil Testing for Construction
To determine soil quality for construction, the soil engineer will have to consider various factors. That’s why they usually conduct different types of soil tests depending on the geological features of the site. The most common ones are:
1. Atterberg Limits Test
This test determines the moisture level at which fine-grained soil transitions between solid, semi-solid, plastic, and liquid. It was named after a Swedish chemist and scientist Albert Atterberg. He noticed that as a soil’s moisture content increases, its consistency also changes.
The test measures three types of limits: plastic limit, liquid limit, and shrinkage limit. Its results will help the engineers predict the soil’s behavior when the moisture level changes.
2. Specific Gravity Test
A soil’s specific gravity refers to the ratio of its solid particles to its water content. It’s computed by getting the ratio of the weight in air of a given volume of soil particles at a stated temperature to the weight in air of an equal volume of distilled water at the same temperature.
The results of this test can help engineers determine the soil’s mineral composition and weathering. It can also be used to calculate the soil’s porosity, degree of saturation, and dry and saturated density.
3. Moisture Content Test
Aside from the solid particles, soils also contain water in varying levels. The moisture content test determines how much water is in the soil which can affect its stability.
There are various methods used to test the moisture content of the soil. The most common of which is the Oven-Dry Method. Under this, the raw soil is weighed before putting it in the oven to dry. Once all the water has evaporated, the soil is taken out and weighed again. The moisture content is then calculated by getting the difference between the weight of the wet soil and the dry soil.
4. Dry Density Test
A dry density test is used to compute the amount of moisture needed for the soil to achieve maximum compaction.
Soil compaction is a common technique used in construction. It’s used to increase the soil’s stability and strength. This allows it to support structures, earthworks, and pavements of varying sizes.
There are two ways to compute a soil’s maximum density: the Standard Proctor Compaction Test and the Modified or AASHTO Proctor Test.
Interested In Cutting Technologies?
For nearly 40 years Cutting Technologies (CTI) has been the go-to demolition contractor for technically demanding, one-off jobs. Our wealth of experience enables CTI to bring “outside-of-the-block” approaches to achieve the impossible. Contractors trust CTI to get the job done right. Take a look at our demolition services on our website.

About The Author
As an avid traveler, Judy Ponio loves to write blogs about traveling and how to save money when making international calls.